Announce New Feature with TM25S
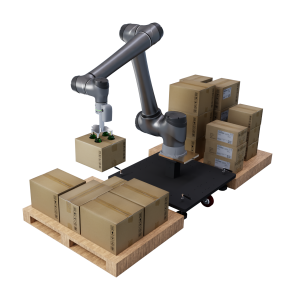
Payload Transition Function
The payload transition function can help you to solve sudden payload transient error. It provides a linear payload interpolation to change smoothly.
Configuration of Force & Torque Monitoring
For unknown payload application, e.g. mix boxes de-palletizing, it is hard to define payload value for robot.
You can select your Force & Torque Monitoring type with robot in “fence-less workspace”, “in collaborate workspace” or “in fence”.
No Need to “Re-Teach” from Beginning
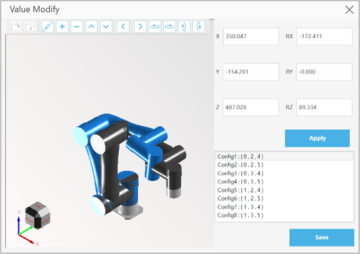
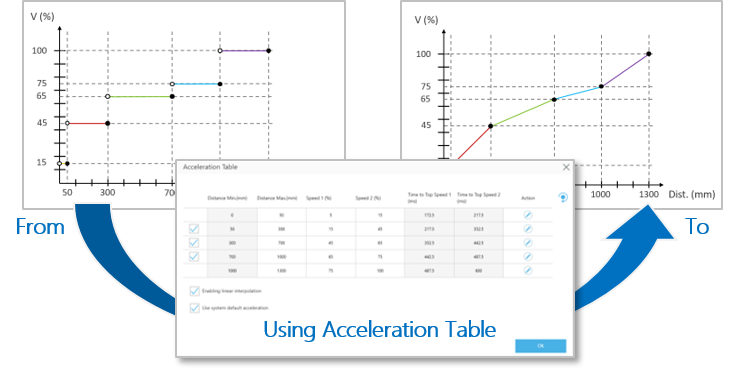
Point & Base Value Modified Function
- Directly modify the Point value as you wish, the target position will be shown in the UI (blue).
- Directly modify the Base value, you don’t need to re-teach the base which saves lots of time!
Smart Acceleration Configure Tool
No Need to “Re-Start” from Beginning
The robot can now recover from error and continue to execute the project after you finish trouble shooting.
You can resume the project from these errors:
- Emergency situation from ESTOP
- Collision situation from Power & Force Limiting
While error happens, robot may drop from Pe to Ps. The robot can be resumed with PTP motion to Pe. Then resume the project by PLAY button.
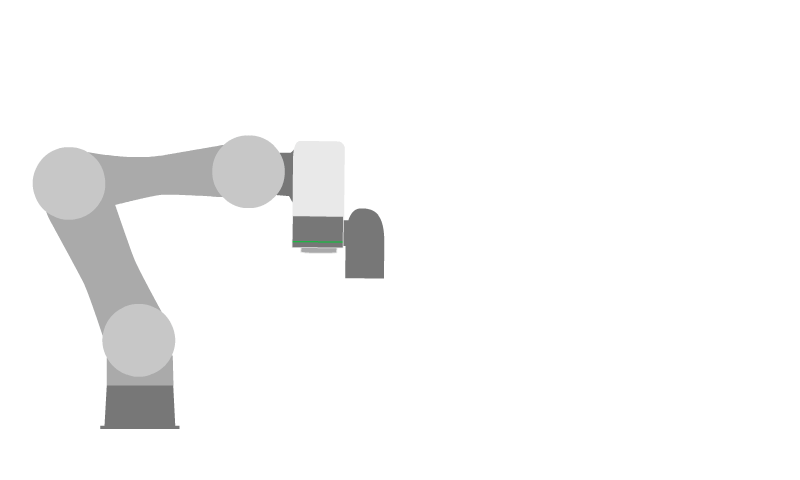
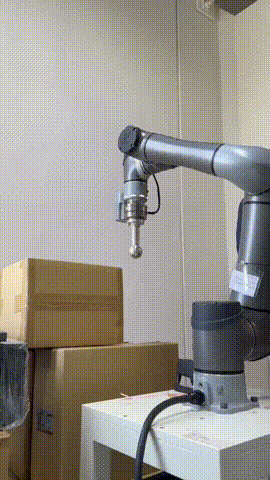
I We Support Your Devices
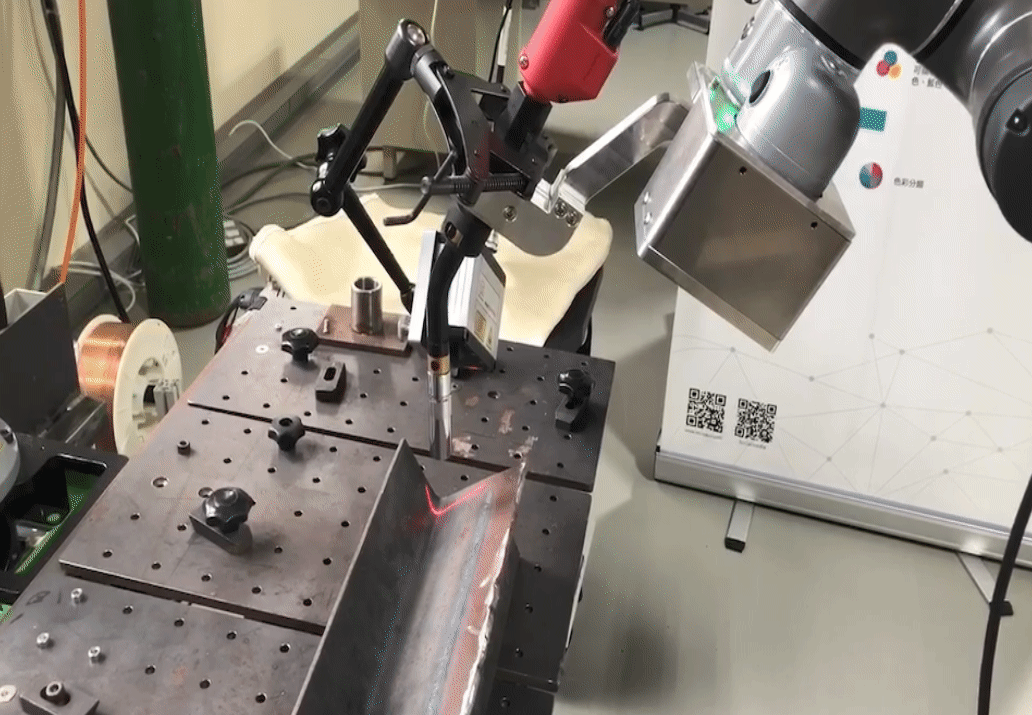
Support Path Offset in Script Command
Support User-Defined EtherCAT Device
Now, we can recognize your EtherCAT devices!
You can add your EtherCAT Digital I/O devices and Analog I/O devices as you wish.

Expand Secondary Development
> TMcraft Service
Customized Daemon program, which always runs at the background.
> TMcraft Node
Customi zed Node UI, which can be used within a Flow Project.
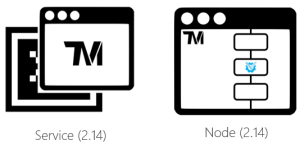
> TMcraft Shell
> TMcraft Toolbar
Customized Toolbar, which can assist user in all sorts of scenarios.
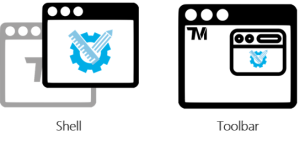
> TMcraft Packer
A stand alone packer to pack your TMcraft plugins.

Test your project with TMflow 2.16 Simulator!
We combine “Client” & “Simulator” together. You can now run TMflow with virtual robot in your PC/NB.
No need to stop the real robot to test your procedure!
1. Both TM AI Cobot and TM AI Cobot S series available.
2. Test your project logic including simulated DI/AI signals.
3. Test your Listen Node and Network Node communication.
4. Test your TMcraft Node, Shell & Toolbar right after development.
5. Simulate your robot programming and motion.
6. Project import and export as from the real robot.
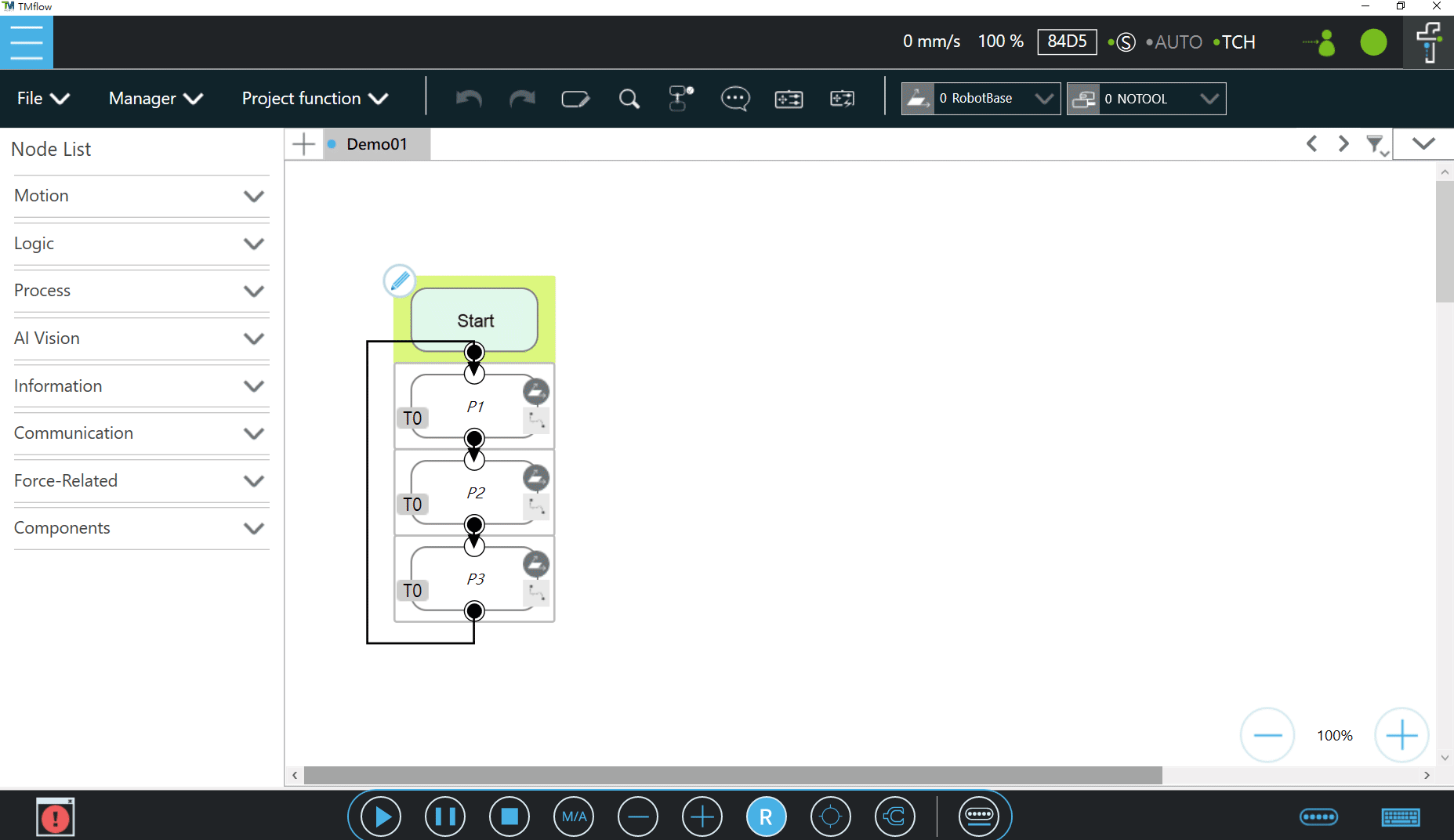
Released by Product Development Dept. Phillip Hsiao