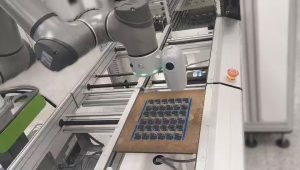
사례 공유: 협업 로봇을 사용한 자동 PCB 접착제 검사
배경 및 고객 요구 사항 전자 제조에서 PCB가 납땜 기계에 들어가기 전에 정확한 접착제 분사를 보장하는 것은 제품 품질에 매우 중요합니다. 한 고객은 분사 결함으로
배경 및 고객 요구 사항 전자 제조에서 PCB가 납땜 기계에 들어가기 전에 정확한 접착제 분사를 보장하는 것은 제품 품질에 매우 중요합니다. 한 고객은 분사 결함으로
배경 및 고객 요구 사항 빠르게 움직이는 전자 제조 분야에서는 포장 전에 제품 품질을 보장하는 것이 중요합니다. 한 주요 고객은 인쇄 회로 기판(PCB)에서 손상되거나 누락된
배경 및 고객 요구 사항 “이 사례의 고객은 대형 전자 제조 서비스(EMS) 공급업체입니다. 이들의 주요 요구 사항은 AI로 훈련된 모델을 활용하여 제품 외관에 대한 고정밀
고객: 다양한 제품에 대한 고품질 맞춤 인쇄 솔루션 제공에 중점을 둔 대만의 선도적인 인쇄 회사. 적용 분야: 인쇄된 팬 제품에 대한 자동 비전 검사. 과제:
고객: 고품질 차량을 생산하는 유명 자동차 제조업체 적용 분야: 자동차 조립 검증 과제: 자동차 제조업체는 생산 공정에서 두 가지 주요 과제에 직면했습니다. 첫째, 5개 이상의
고객: 수공 슬리브 구성품의 선도적 제조업체 응용 프로그램: 스크린 인쇄 금속 주조물의 자동 결함 감지 과제: 고객은 미터법과 영국식 단위를 구별하는 데 사용되는 고유한 스크린